Dealing With an Aircraft Emergency
A couple weeks ago a new client called me and told me of his recent scary experience. He had been flying his Cherokee 180 the previous day when the engine suddenly became very rough and lost significant power. He was at 13,500 MSL 50 miles west of Wendover, Nevada. A quick decision was made to turn toward the interstate and head back toward Wendover. At least over the freeway there would be places to land if he had to and help would be nearby.
Greg and his brother were on their way for a business trip in Sacramento when the problem occurred and now they were losing altitude wondering if they would even make it back to an airport. Declaring an emergency with flight following would alert the authorities and keep their location at least until the lost radar. Switching fuel tanks, richening the mixture and applying carb heat didn’t help. The engine irregularly chugged along at about 1500 RPM threatening to quit at any moment. The 50 mile stretch to the airport took forever and when the field came into sight Greg reported he was making a straight into runway 12 with an emergency.
The landing was made uneventful and the stress and fear changed to happy and thankful to be on the ground safely.
Arrangements were made to hangar the airplane and the airport manager drove Greg and his brother back to their home base at Skypark, about 120 miles away.
No search parties, no bent metal, and no injuries. Everything had turned out good and thoughts now turned to getting the plane fixed and back home. As I listened to the story I went into troubleshooting mode and thought through all the possibilities. I hoped on Greg’s behalf it would be something simple but sort of knew it sounded more serious. We made arrangements to fly out the next day with a handful of parts and some tools including a borescope. Hopefully, we would be able to find the problem, it would be simple, we could fix it and bring the airplane home all in one trip.
My 210 needed some exercise since I hadn’t flown it for awhile so I was glad to have an excuse to fly it. The 48 minute flight was perfectly smooth in beautiful sunny skies and Greg and I had an opportunity to get to know one another. I also got the full story of his adventure the day before. It seems like pilots always want to know the details in these types of stories with a hope of learning something that may benefit them in the future. At least, that is how I feel.
We rolled up to one of the old hangars where I could see the pretty little Cherokee sitting inside. Wendover was an important air base during World War II where training was done for the crew who dropped the Atomic Bomb on Hiroshima. The control tower, barracks, officers club and hangars are still there and ongoing efforts are being made to preserve and restore them. I am always intrigued as I consider the bustling activity that went on there in the 40’s. I walked into the hangar and gazed up at the big wooden roof trusses and the paned windows and almost felt like I was going back in time.
Greg keeps his plane perfectly clean and it looked nice sitting in the corner of the hangar with the sunlight streaming in.
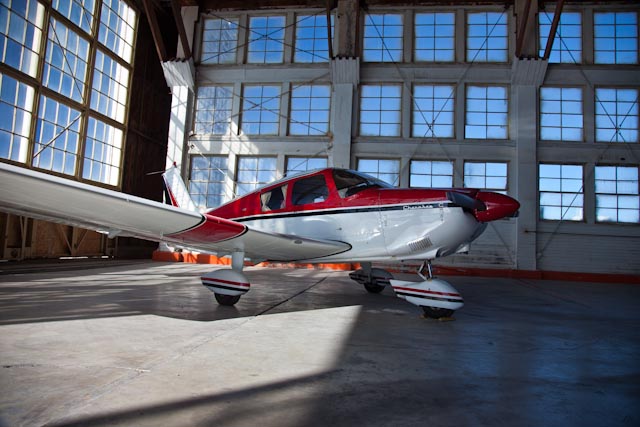
Before even taking the cowling off I checked to make sure the mag switch was off, then pulled the prop through 4 revolutions. On what should have been the 4th compression stroke the propeller had no resistance at all confirming my suspicion that something inside the engine had come apart or broken. We quickly removed the cowl and pulled the top spark plugs out. When we removed the number 1 plug it showed signs of damage leading me to know this is where the problem was. Any time loose parts start rattling around in the cylinder the spark plugs are ruined almost immediately.
I put the neck of the borescope into the cylinder and could instantly see what the problem was. The exhaust valve was missing. Somehow the head of the valve broke off and was completely gone. I looked carefully at the piston and could see extensive damage in the form of dings and dents where loose parts had been impacted between the piston and cylinder head each time the piston reached the top of its travel. Luckily I couldn’t see any holes where it had broken completely through. Had this been the case we would have had a more serious problem with metal in the oil.
Obviously, we were not bringing the airplane back home with us. I made a list of parts and tools I thought we would need and removed the oil filter so we could cut it open at the shop to verify there was no metal in it. We loaded back in my plane and were soon headed home.
I ordered an overhauled cylinder and within a few days was ready to head back to do the repair. We arrived, tools and parts in hand and worked together to remove the cylinder.
As I pulled the exhaust stack from the affected cylinder I shined my flashlight into the muffler and could easily see fragments of the broken exhaust valve. The inner baffles were intact in the muffler and had captured the pieces. As near as I could tell about ¾ of the valve head was there in 3 separate pieces. It must have taken a lot to break it up. Now I wondered where the remainder of the valve had ended up. Once the cylinder came off it was apparent. It was lodged into the piston head having been pounded into it. Luckily it had not poked a hole in the piston which often happens. I did notice however that the back side of the piston surface was fractured and it would not have taken much more before a gaping hole would have occurred. Had that happened our job would have been dramatically different with metal contamination in the oil system as well as possible damage to other internal engine components from the debris. The entire engine would likely have had to be disassembled.
Luckily all we had to do was install the new cylinder with a couple new spark plugs, change the oil and be on our way.
The total process from this point only took a couple hours at which time we moved the airplane outside, took a final look over and test ran the engine. It started right up and ran perfectly throughout a normal run up procedure. We shut it down and inspected the engine assembly for any possible leaks or other abnormal conditions. I found one clamp on the exhaust I had not tightened but no leaks or other problems. After fixing the clamp the cowl went on and one more quick run up was done at full power just to be sure everything was operating correctly.
Greg posed for a photo in front of the old original control tower and then went in to pay for his hangar fees.
We agreed to switch to 122.75 once outside the traffic area to communicate with each other then jumped in to the two aircraft and took off. I followed for awhile and made a few photos as we flew together, then powered up and sped off for Skypark. We both arrived safe and sound with a satisfaction of having done a good job.
Fixing airplanes is fun for me and I like being able to help people. I also always enjoy going off somewhere to rescue pilots and planes. Nice warm sunny conditions, an interesting location and flying my own airplane make it all that much better.
I have seen a small handful of similar valve failures as this one over the years. I don’t really have an answer why it happens but it is relatively uncommon. Airplane engines are very reliable overall, but like anything mechanical they are subject to wear and tear. We generally have some awareness of these wear and tear conditions through routine inspection and testing procedures. Unfortunately we don’t often have much foresight for failure and can only prepare for such circumstances by proper training and thoughtful consideration of “the what ifs”. I think that our awareness of our surroundings and aircraft emergency procedures is paramount if we are to be pilots. Training, proper maintenance, good judgment and situational awareness need to be constantly practiced. Manufactures recommend overhaul, inspection and replacement schedules on almost all major components of the aircraft. Some of these suggestions are more important than others and it can be difficult for pilots and mechanics alike to know when and what the important ones are. Being educated and involved is the key. Find those in the industry that can give you good information and read the publications that are available to you, then evaluate all the information and make the best decisions concerning maintenance as you can. This does not mean you will never have a problem and Greg’s experience with the broken valve is a perfect example of that. His engine and components were all within the manufactures overhaul time limits. What we try to do is minimize the risks as best we can with the information we have and then try to fill the rest of the gaps with good skills, good judgment and a little luck.
This was a very enjoyable article Jim. Thanks!
What about the cylinder head? It looks damaged and should probably be replaced pretty soon…